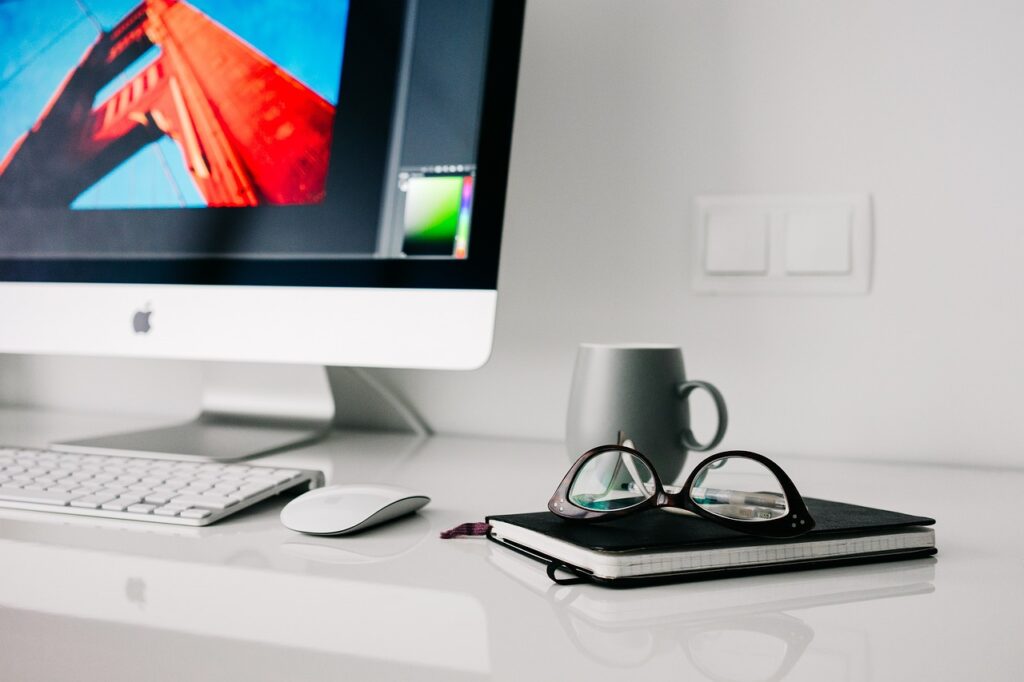
How to Launch a Successful Custom Injection Molding Project
You have your idea, you’ve secured room in the budget, and now you’re ready to launch your custom injection molding project. Whether you’re new to this field or looking to refine your approach, this guide outlines the essential steps to successfully launch your custom injection molding project.
1. Understand the Process of Contract Injection Molding
What is Custom Injection Molding?
Custom injection molding is a manufacturing process used to produce parts by injecting molten material into a mold. This technique is ideal for producing high volumes of identical parts with precision and repeatability.
Contract injection molding refers to outsourcing your project to a specialized company. Rather than clear the immense capital hurdle of buying your own machines and outsourcing the injection mold yourself, you can contract with a company with extensive industry knowledge to handle the manufacturing of your project. This is an effective way to leverage expert knowledge, advanced equipment, and cost-effective production.
2. Design Your Part
Before moving to the injection mold process, it’s crucial to finalize your part design. This involves considering the shape, and functionality of the part, but also making sure that your component is designed for manufacturability. Collaborate with designers and engineers experienced in custom injection molding to ensure your design is optimized for manufacturability. Montrose Molders works with industrial designers that have decades of experience in refining part designs for optimal performance and minimal cost.
3. Select the Right Thermoplastic
The material choice is pivotal in determining the functionality and durability of your part. Consider factors like strength, flexibility, and environmental resistance. Your injection molding partner can provide valuable insights into the best materials for your specific application. This link provides a guide to the characters of many different thermoplastic resins used in the injection molding process.
4. Creating the Injection Mold
An injection mold is a custom-made tool used in the injection molding process. It’s designed to precisely form the part you’re producing.
Ensure your mold is designed and manufactured with the highest precision, as this will directly impact the quality of your final product. High volume injection molding demands molds that can withstand repetitive cycles without degradation.
The resource in this link will provide guidance on the classification of injection mold that is right for your project. Click here for information on the SPI mold finish that is appropriate for your project.
5. Prototyping and Testing
Before full-scale production, create prototypes to test the design, material, and functionality of your part. Depending on your project, this step may or may not be necessary to preview problems before spending capital on a production quality Class 101 tool.
Prototyping options include FDM (3D Printing), SLA, or “soft” aluminum molding. Speak with one of our technical representatives for guidance on which type of prototyping is right for your project.
6. Production and Automation
For large-scale production, high volume injection molding is your go-to process. It ensures consistent quality across thousands or even millions of parts. For these projects, consider incorporating automation in your injection molding process for enhanced efficiency and accuracy. Automation minimizes human error, speeds up production, and can lead to cost savings, especially in high-volume projects.
7. Quality Control and Optimization
Quality control is paramount in custom injection molding. Implement rigorous testing and quality assurance processes to ensure each part meets your standards. Continuously seek ways to optimize the process for better results and cost-effectiveness. Fortunately, Montrose Molders is ISO9001 certified and has put into place rigorous inspection checkpoints to confirm that all components are produced and packed in accordance with customer specifications.
8. Assembly and Post-Processing
If your project requires assembly of multiple parts or specific post-processing steps like part-to-part assembly, part-to-electronic assembly, sub-assembly, or part decoration. Ensure that your injection molding partner can handle these additional requirements or collaborate with other specialists who can.
9. After-Sales Support
The project isn’t company when it ships to its destination. Choose a contract injection molding partner who offers robust after-sales support. This includes assistance with any issues post-production and potential for future project collaborations.
—
By following these steps and leveraging the expertise of a seasoned injection molding partner, you can successfully launch your custom injection molding project. Remember, every step from design to distribution plays a crucial role in the success of your product.
Speak with one of our experience technical representatives to find out how Montrose Molders can help you success in your next project.