Whether you’re designing an industrial component or a consumer product, the success of your part in the field depends on sound part design. Failure to use best practices will prevent your part from meeting the functional and aesthetic requirements of the application.
Well-designed parts are not only durable and sleek, but also cost effective to produce. When designing your next component, take the following part design considerations into account.
Material Selection:
The first step in designing any injection molded part is to select the right material. There are many different types of plastic materials available, each with its own unique properties. Some factors to consider when selecting a material include:
- Strength and stiffness: The part needs to be strong enough to withstand the forces it will be subjected to in use.
- Flexibility: The part may need to be flexible, depending on its application.
- Durability: The part needs to be durable enough to withstand wear and tear.
- Chemical resistance: The part may need to be resistant to certain chemicals, depending on its environment.
- Cost: The cost of the material is also an important factor to consider.
Radius
Radii are used to smooth out sharp corners on injection molded parts. This is important because sharp corners can cause stress concentration points, which can lead to part failure. Radii should be at least 0.25 times the wall thickness of the part.
It is also important to note that sharp, radii-free corners can drive up the cost of the injection mold because sharp corners must be burn via EDM rather than machined via CNC.
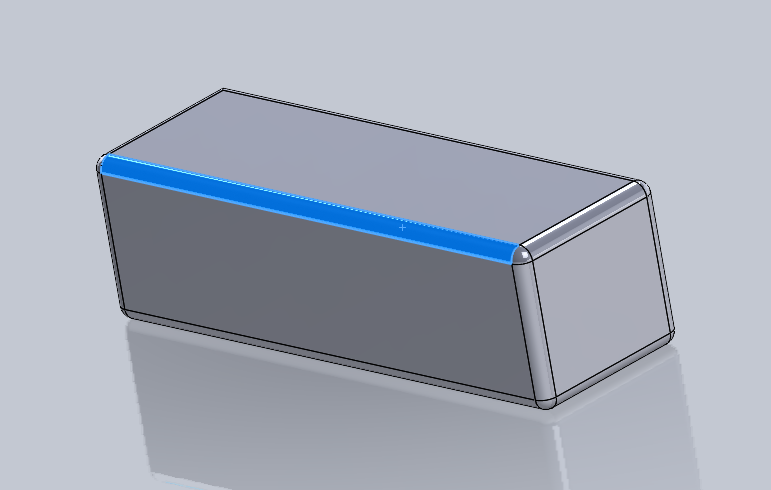
Wall thickness
The wall thickness of an injection molded part should be as uniform as possible. This is important to prevent sink marks and warping. The ideal wall thickness will vary depending on the material and the part’s geometry. Below is a wall thickness guide chart.
Material | Recommended Wall Thickness |
ABS | 0.045 – 0.140 in |
Acetal | 0.030 – 0.120 in |
Acrylic | 0.035 – 0.120 in |
Nylon | 0.030 – 0.115 in |
Polycarbonate | 0.040 – 0.150 in |
Polyester | 0.030 – 0.125 in |
Polyphenylene Sulfide | 0.030 – 0.180 in |
Polypropylene | 0.030 – 0.150 in |
Polystyrene | 0.035 – 0.150 in |
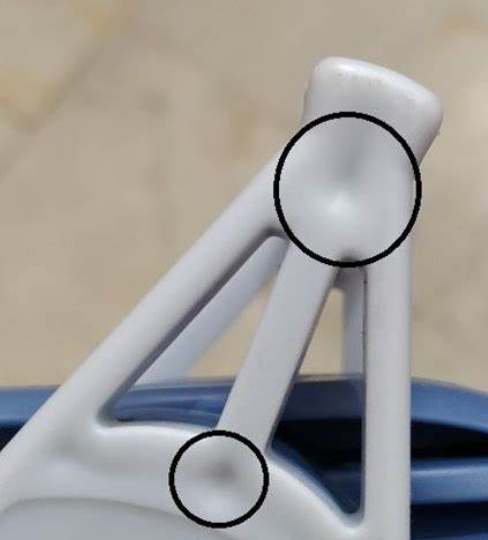
Gate location
The gate is the opening in the mold through which the molten plastic enters the cavity. The gate location should be chosen to minimize flow length and to ensure that the part fills completely. It is also important to avoid placing the gate at a location where it will cause cosmetic defects. While gate design and location is mainly a tooling consideration, it is recommended that it be considered by the industrial designer.
There are several different gating types that can be considered: edge, fan, sub, banana, valve and hot drop to name a few.
Draft
Draft is the angle of the part walls relative to the parting line of the mold. Draft is necessary to allow the part to be ejected from the mold without damage. The recommended draft angle is 0.5-1 degree.
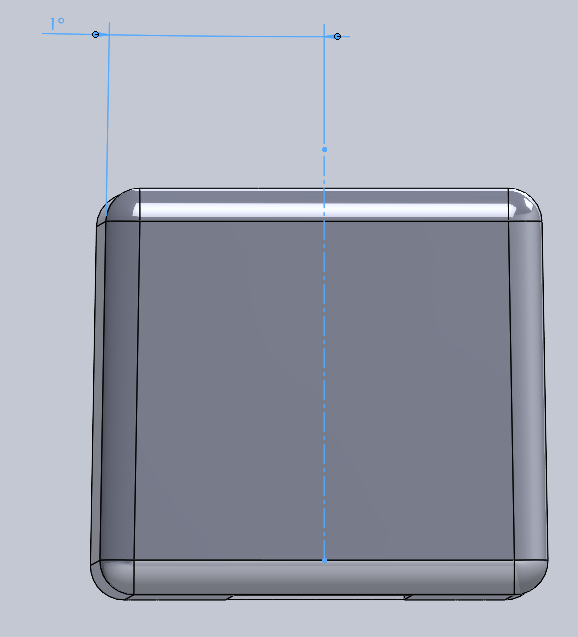
Undercuts
Undercuts are features on a part that prevent it from being ejected from the mold. Undercuts can be avoided by designing the part so that it can be ejected from the mold without the need for undercuts. If undercuts are necessary, they can be accommodated by using side actions or collapsible cores in the mold, but these features drive up the cost of a tool.
Additional tips
- Avoid designing parts with complex geometries. Complex geometries can make the mold more expensive and difficult to manufacture.
- Use ribs and bosses to reinforce areas of the part that require additional strength.
- Design the part so that it can be easily ejected from the mold.
- Consult with a plastic injection molder early in the design process to get feedback on your design.
By following these tips, you can design plastic injection molded parts that are strong, durable, and cost-effective.
For more guidance and information, reach out to our technical staff by clicking here.